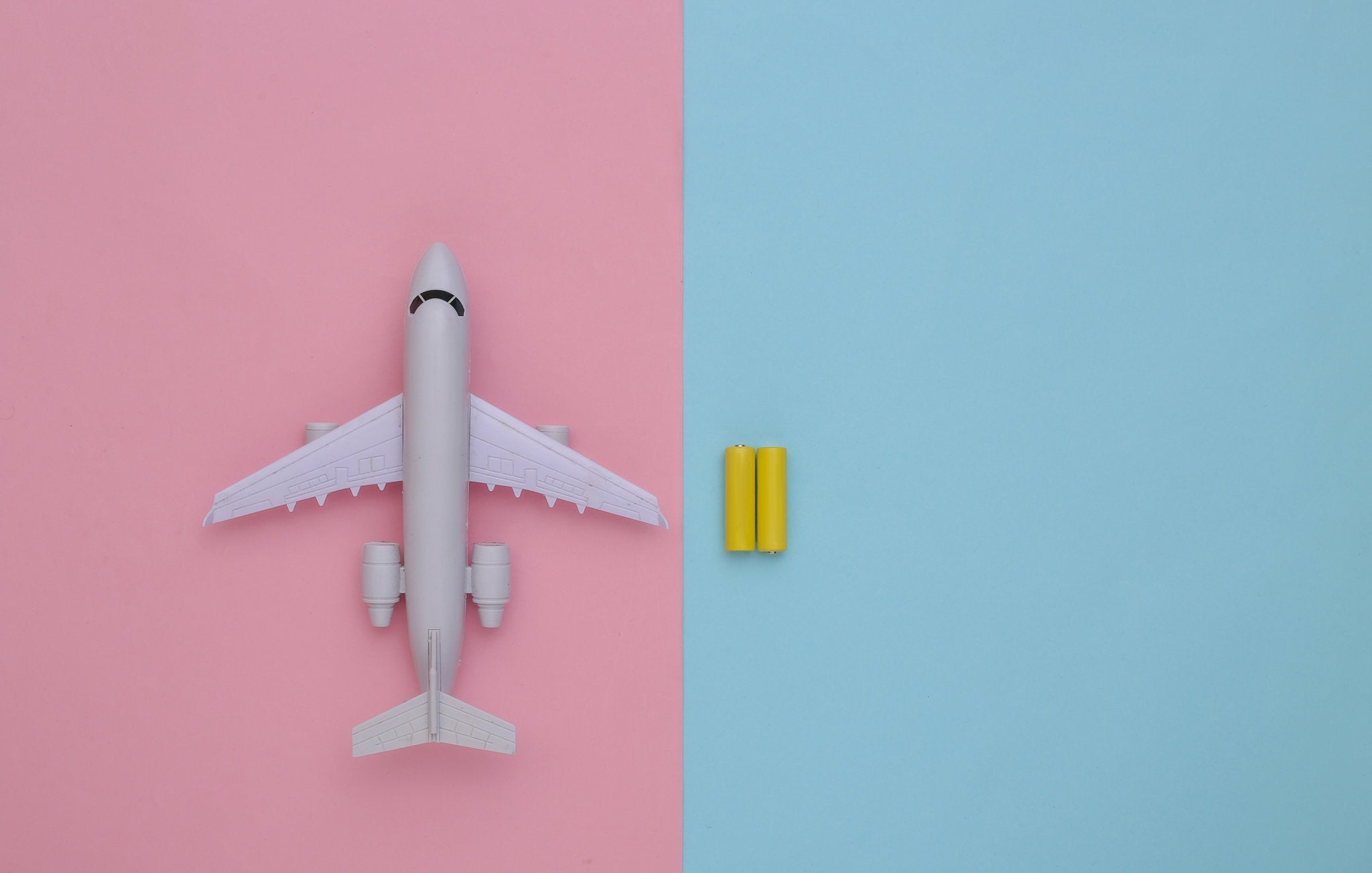
Today’s lithium-ion battery technology is unable to support the mainstream development of electric flight. We’re already able to use lithium-ion batteries to complete short flights in small craft, but this technology does not provide the performance and safety requirements to make electric flight an option for anything more than unregulated, hyperlocal travel for small numbers of passengers.
Aircraft batteries have different requirements for land vehicles. For example, they need to be as light as possible while still being able to store the huge amounts of energy required to power flights and be able to quickly discharge large amounts of this energy when needed.
The aircraft could also benefit from a wider temperature of operation, especially at high temperatures, and the batteries also need to be more inherently safe than their land-based equivalents, as the dangers of an in-flight fire are more serious than one on the ground.
The holy grail of battery design
The Solid-state Architecture Batteries for Enhanced Rechargeability and Safety (SABERS) initiative is currently working to develop a battery that meets these goals to usher in a new era of power storage for electric air travel.
A joint venture between NASA, Georgia Institute of Technology, Argonne National Laboratory, and Pacific Northwest National Laboratory, SABERS researchers have been using different materials and novel construction methods to develop a new kind of battery.
“We wanted to use and combine currently available technologies in different and unique ways, using some of NASA’s core material science techniques and technologies it’s created,” says Dr Rocco Viggiano, principal investigator for SABERS at NASA’s Glenn Research Center in Cleveland, Ohio.
“There are a lot of processes and techniques in place from lithium-ion and we wanted to make use of these, so we didn’t have to reinvent the battery from scratch.”
Materials in battery technology
SABERS’ goal is to create a scalable battery three times as energy-dense as current lithium-ion cells, inherently non-flammable, lightweight, and with a fast recharge speed.
To achieve this, the team turned to materials that had – until that point – not been used together in battery systems and developed a solid-state sulphur-selenium battery.
Instead of housing each cell inside its own casing, this battery is made up of individual cells that can be stacked vertically inside a single casing, which is called a bipolar configuration. Each cell consists of a lithium metal anode, a solid-state electrode, and a sulphur and selenium cathode, from where the energy is derived.
Here the particles are arranged in a graphene mesh: a NASA-created component called holey graphene, which has a high level of electrical conductivity and is ultra-lightweight.
This solution has not only increased the battery system’s energy density and reduced its overall weight, but also supports scalable and affordable manufacturing.
“From a supply chain standpoint, the US is the second largest supplier of sulphur in the world – it’s an inexpensive waste bi-product of fossil fuel refinement,” Viggiano says. “We’re using it as the battery’s primary component, which is also great from a sustainability point of view, as we’re reducing its impact on the environment.”
SABERS: the test results so far
Given that aircraft are subjected to much more extreme environments, this new battery needed to be more robust than its predecessors. This was why a solid-state design was chosen, as these types of batteries don’t catch fire or overheat as quickly as their lithium-ion counterparts, and can also perform better in stressful environments.
For example, the lack of flammable liquids in its design means the new battery can safely reach much higher temperatures than the lithium-ion design.
“Previous cells can go up to 60°C, whereas our cells have been regularly tested up to 120°C, and we’ll be going to 150°C next,” Viggiano says. “This is pretty important for the application of electric flight, as you’d usually have a heavy thermal management system to keep the battery from going into thermal runaway. By saving weight here, we’re also able to get additional range.”
Tests on SABERS’ prototype have shown that the battery can even keep operating if severely damaged on impact, which is a critical factor for aviation use.
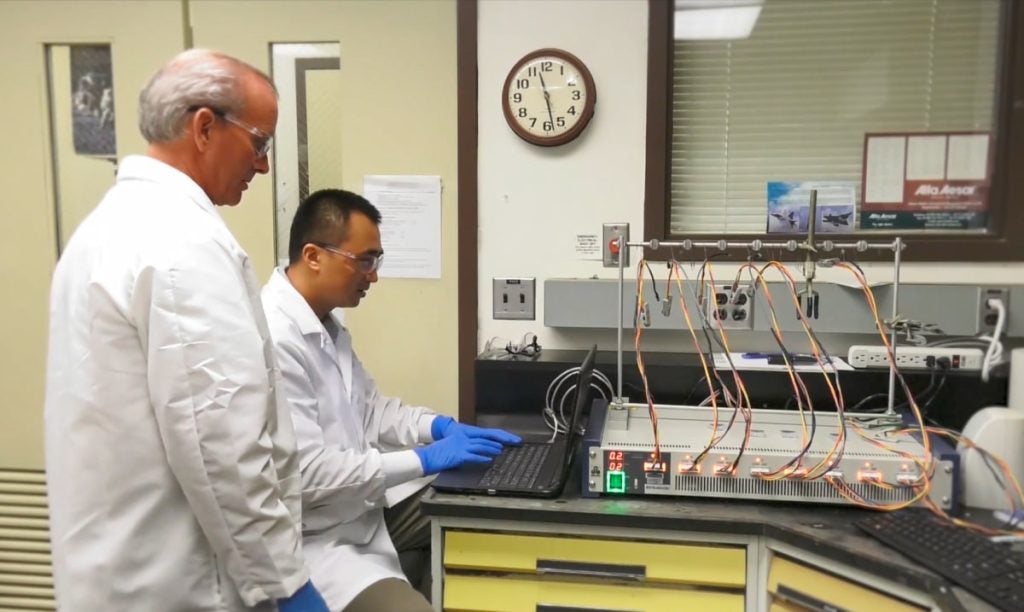
“There are always unexpected findings in research, and for us, well we weren’t quite expecting this level of safety. We cut a battery in half to test that it wouldn’t catch on fire, which it didn’t. But we were very surprised to discover it would continue to operate for a small time after it had been damaged,” adds Viggiano.
Currently, SABERS’ demonstrator battery has achieved two times the energy density of previous battery designs and the researchers are now looking at new ways to further improve on this.
“Our initial target was 500Wh/kg, approximately two times the energy density of lithium ion. At first, we weren’t sure if we’d be able to achieve that, but early on we reached an even higher value, 586Wh/kg. That led to some excitement around the other ways we could improve this further. I now believe we can get to three times the energy density,” Viggiano enthuses.
Work in progress
Researchers continue looking for ways to improve the battery’s discharge rate. In the past year they’ve been able to increase this rate first by a factor of ten and then by another factor of five, inching them closer to their goal of powering a small plane’s launch.
Viggiano cautions that there’s still a very long way to go before SABERS’ battery would be able to power single-aisle small aircraft on flights of up to potentially 250 miles (another of the team’s goals).
Currently, researchers are using in-depth computational modelling and machine learning on a digital twin to assess and predict ways they could improve the battery’s design further, in order to meet the energy demands such an objective would require.
“I don’t want to give the impression that this is something that’s going to be around tomorrow. The good news is that we can see a pathway to achieving the outcomes we want, but it will still take a lot of work,” he concludes.