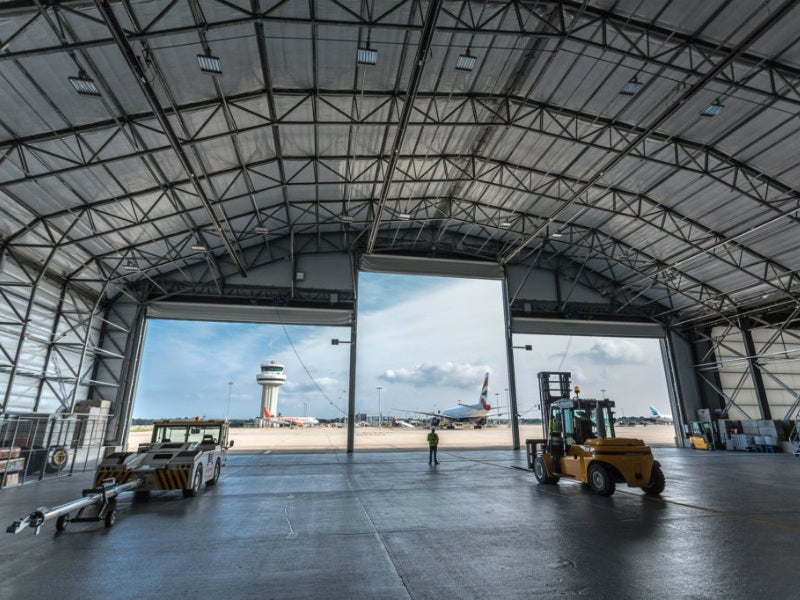
With the fast-changing nature of the maintenance, repair and overhaul (MRO) industry, companies need must be able to adapt, including with the choice of hangar solution.
Compared to traditional hangars, modular designed structures are designed in a way to reduce the overall structure weight. They are also flexible enough to be moveable, extendable and relocatable, becoming a greater long-term asset. To further reduce the overall structure weight and to support the ease of construction, aircraft hangars can be clad with a lightweight, but robust PVC fabric. An industry leader providing these types of new hangar systems is Rubb Group.
Rubb hangars are designed to British standards or Eurocodes with regards to wind speeds and snow loadings. Like a traditional hangar, Rubb structures are designed to accommodate the full weight of snow acting on the roof. As they are designed to meet these codes, Rubb structures are a direct and comparable alternative to a traditional hangar.
Constructing such an alternative hangar system can be done with ease. All manufacturing is completed off-site. The framework and cladding are then shipped to the client’s chosen location in a specific order, to follow and maintain the installation plan. The framework is constructed at ground level and lifted up in place, then bolted together. The PVC membrane cladding is lifted over the steel structure and then anchored and tensioned to the foundation. Manufacturing and construction times can overlap to reduce the overall project timescale.
The fabric that is used to cover Rubb aircraft hangars is a tough PVC impregnated polyester fabric. The material is tested with respect to tensile strength, elongation, tearing strength, bursting strength, coating adhesion and resistance to flexing, according to BS 3424. Translucency and thermal advantages are key when using PVC fabric. High translucency and a pure white colour improves visible light and appearance, for comfort and safety, also reducing energy costs and increasing sustainability. The fabric is flame retardant and self-extinguishing to BS 5438 Test 2B to improve fire safety. Lightweight fabric has a manufacturer’s warranty of ten years, but Rubb hangars have been in use around the world, and have proven to last more than 40 years with the original PVC sheets.
To help create the perfect MRO working environment, Rubb hangars can be insulated using Thermohall PVC cladding technology. This comes in a number of thickness options, but Rubb would recommend 150mm Thermohall for an aircraft hangar, which provides a U-value of 0.25W/m²K, meeting British Building Standards.
Rubb hangars, like traditional hangars, need suitable foundations to take structure loadings. Depending on the existing surface, Rubb would need a minimum of a concrete upstand ring beam or concrete foundation pads to support the structure only. If these types of foundation arrangements can be achieved, instead of a completely new slab, this significantly reduces project costs and speeds up construction time.
Rubb supplied easyJet at Gatwick Airport a twin span, semi-permanent, modular hangar, measuring 91.5m × 60m. Rubb was appointed the main contractor for the complete project, overseeing the groundworks to internal fit out. The first sections of the modular steelwork were constructed on 14 December and by 19 May easyJet was able to introduce the first aircraft into the hangar. For a project of this size, and within a challenging and complicated working environment, it was great to see everything come together with great success.
Brendan McConnellogue, easyJet’s head of maintenance, commenting on the project, said: “The Rubb team who worked on site were absolutely first class. The successful delivery of this project, which has been challenging both in terms of scale and its timeline, is another example of what can be achieved through easyJet’s innovative and lean approach, not only meeting a tight timeline, but also creating strong sustainable partnerships to deliver market-leading operational performance.”