Holger Pfriem, Dafo Asia managing director and Dafo Vehicle Fire Protection business manager, explores the risks associated with electric ground support equipment and how to minimise these to ensure maximum safety and minimal damage and downtime.
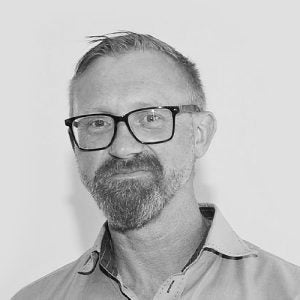
The aviation industry is seeing unprecedented demand. Excluding the impact of the coronavirus pandemic, air transport has seen a sustained increase in demand, which is expected to continue over the next few decades.
Under intense scrutiny from governments around the world, the whole industry is looking for new, innovative solutions to reduce carbon footprint and overall environmental impact. As part of this, many organisations are turning to electricity as an alternative, more sustainable fuel source for all ground support equipment and machinery.
However, this is bringing about new fire risks, which can have significant and costly consequences if not addressed effectively.
The electric impact
Whether it’s transfer buses, push-back tractors, or refuellers, the aviation industry is actively adopting electric alternatives to the traditional, combustion engine vehicles and machinery operating on the ground to enable its continued air operations.
This is undoubtedly having an impact on overall environmental impact, but it is also bringing about new fire risks – which aren’t effectively addressed with traditional fire detection and suppression techniques.
The majority of electric vehicles (EVs) and machinery used for ground support operations are powered by lithium-ion (li-ion) batteries. Although fire risk is arguably lower for EVs vs internal combustion engine vehicles, the consequences of any fire can be significantly greater.
There are four main risks associated with li-ion batteries:
- Overcharging or undercharging: where battery power is drained too quickly or charged too rapidly.
- Mechanical influences or failures: these can be caused by a number of factors, such as a vehicle collision, for example.
- Exposure to heat: li-ion batteries are extremely sensitive, meaning temperatures need to be continuously monitored and controlled. If operating close to external heat sources, for example, those caused by a fire surrounding the vehicle, or in other areas of the vehicle itself, the battery is at greater risk.
- Production issue: where particles are able to enter battery cells. As li-ion batteries are compact, with thin cell layers, any particles – no matter how small – can cause internal component damage.
Each of these risks can lead to internal short-circuits within the li-ion battery. This is the primary cause of thermal runaway – an extremely dangerous state, where rapid battery temperature increases can result in fire, toxic gas emissions, and large explosions.
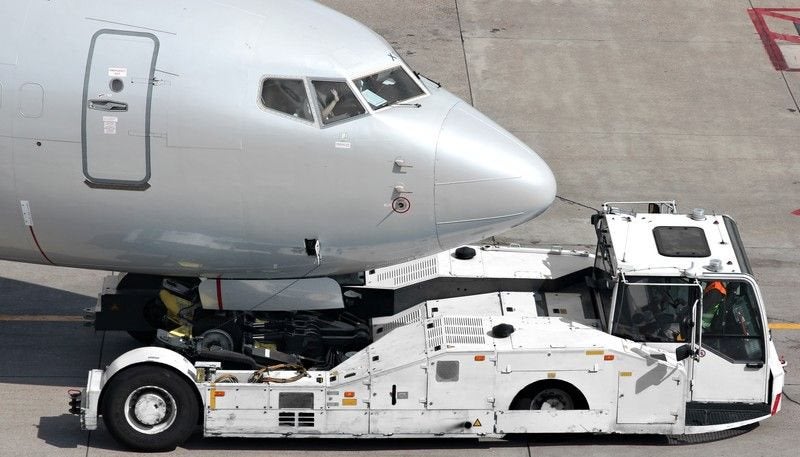
These significant temperature increases are a critical signal that thermal runaway is already underway. Once temperatures have begun to rise, it can be extremely difficult to control or reverse the process.
Ahead of temperature increases, li-ion batteries will emit toxic gases, as a pre-cursor that they’re entering thermal runaway. At this stage, if it’s detected successfully, with the right detection and suppression solution, the process can often be reversed.
As traditional fire detection and suppression systems are often only able to identify thermal runaway by detecting rapidly increasing temperatures, there’s a clear need for a unique protection solution. That is, one which is able to detect toxic gas emissions ahead of temperature increases.
A much bigger issue
For airports, the risk of thermal runaway poses a much larger threat, due to the value of surrounding equipment and aircrafts and the number of passengers being transported through the airport apron at any one time.
Ground support equipment is often in operation close to aircrafts, airport workers, and passengers. This means any fire risk is amplified, as it can have significant consequences for surrounding people, valuable assets, as well as the environment. This extensive impact of ground support equipment fires is well documented.
Airports have a responsibility, and financial need (when it comes to downtime and the costs associated with that), to ensure the safety of their ground support equipment and machinery – whether powered by electric or combustion engines.
How can airports minimise fire risks?
Ensuring safety and preventing unnecessary downtime starts by understanding your individual risks. It’s not just about considering electrical equipment, but all equipment and how it operates.
Once you understand the different risks, you can begin to develop a bespoke fire protection solution, which addresses each of these effectively.
When it comes to electrical equipment, you should also consider ensuring equipment is disconnected from charging points once fully charged.
Another thing to consider is the location of charging stations, and where the power for these stations is stored and how it’s protected. The larger battery units, which store power for individual vehicles will also be subject to the same risks, on an arguably larger scale.
Isolation/quarantine protocols for damaged electric vehicles is another important consideration, including monitoring solutions to identify thermal runaway risk before it causes temperature increases.
Suppressing your airport’s fire risks is about considering your entire operation, including how your vehicles and machinery operates in context, then developing a tailored protection solution, which addresses the pertinent risks effectively – maximising safety and minimising downtime.