
Turbomeca has started production of helicopter engine components using a 3D printing process at its facility in Bordes, France.
The Bordes facility is said to be one of the first-of-its-kind plant in aerospace propulsion industry to use additive manufacturing technology.
The company is using selective laser melting (SLM) techniques to produce fuel-injector nozzles for its Arrano test and production engines.
Ardiden 3 combustor swirlers will also be produced using the same manufacturing process.
Unlike traditional manufacturing processes, additive manufacturing process produces parts to a 3D computer-aided design model.
The process builds up to 100 micrometres thick layers of fine metal powder to produce complex-shaped components.
How well do you really know your competitors?
Access the most comprehensive Company Profiles on the market, powered by GlobalData. Save hours of research. Gain competitive edge.
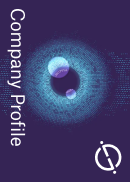
Thank you!
Your download email will arrive shortly
Not ready to buy yet? Download a free sample
We are confident about the unique quality of our Company Profiles. However, we want you to make the most beneficial decision for your business, so we offer a free sample that you can download by submitting the below form
By GlobalDataThe SLM technique involves a computer-controlled laser that shoots beams onto a nickel-based super-alloy powder bed, to melt the metal in the desired areas.
Using additive manufacturing technique, the Arrano fuel-injector nozzle is made from a single piece of material and exhibits advanced injection and cooling functions, Turbomeca said.
The company already operates SLM equipment at the plant, and plans to install more machines in the coming years.
The latest move is part of Turbomeca’s ‘Future Line’ programme, which is designed to improve the company’s manufacturing capabilities.
As part of the programme, Turbomeca new processes such as additive manufacturing and high velocity oxy-fuel coatings, to improve its compressor and turbine blade manufacturing capabilities at Bordes.
Image: Turbomeca is using selective laser melting techniques to produce Arrano engine components. Photo: courtesy of Rémy Bertrand / Safran.