
Lockheed Martin has carried out the final static test of a heat shield, which will form part of the two-part aeroshell to encapsulate Nasa Jet Propulsion Laboratory (JPL)’s Mars 2020 rover mission.
In the test, the flight hardware structure of the shield was exposed to real flight-like thermal climates to assess the physical integrity against extreme atmospheric conditions of space travel.
Lockheed Martin is contracted to deliver a two-part aeroshell system with a 4.5m diameter for Nasa’s Mars mission next year. The heat shield will protect the rover while it enters the Martian atmosphere.
The heat shield aerodynamics will enable the spacecraft to slow down from a speed of 19,300km/h.
Lockheed Martin Mars 2020 Aeroshell programme manager Neil Tice said: “Our experience building aeroshells for Nasa Mars missions does not mean that it is ‘easy’.
“Tests like this structural test are absolutely essential to ensuring mission success in the long-run.”
How well do you really know your competitors?
Access the most comprehensive Company Profiles on the market, powered by GlobalData. Save hours of research. Gain competitive edge.
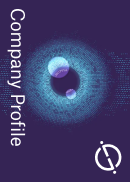
Thank you!
Your download email will arrive shortly
Not ready to buy yet? Download a free sample
We are confident about the unique quality of our Company Profiles. However, we want you to make the most beneficial decision for your business, so we offer a free sample that you can download by submitting the below form
By GlobalDataDuring the test, Lockheed Martin engineers used vacuum pumps to simulate around 140,000lb of pressure on the heat shield structure. The structure was tested to 120% of the expected flight load that the structure will experience during the entry phase.
In addition, the engineers and Nasa Langley Research Center used a new tool called Photogrammetry or Digital Image Correlation, instead of conventional strain gauges and extensometers.
It enabled the team to monitor full-field strains and displacements throughout the whole visible area of the structure in real-time.
A set of digital cameras was also deployed during the test to capture any changes in the pattern. It also enabled to generate a 3D map of displacements and surface strains with an increase in the applied load on the structure.
After the completion of all tests and environmental testing, the full heat shield will be attached to the backshell.