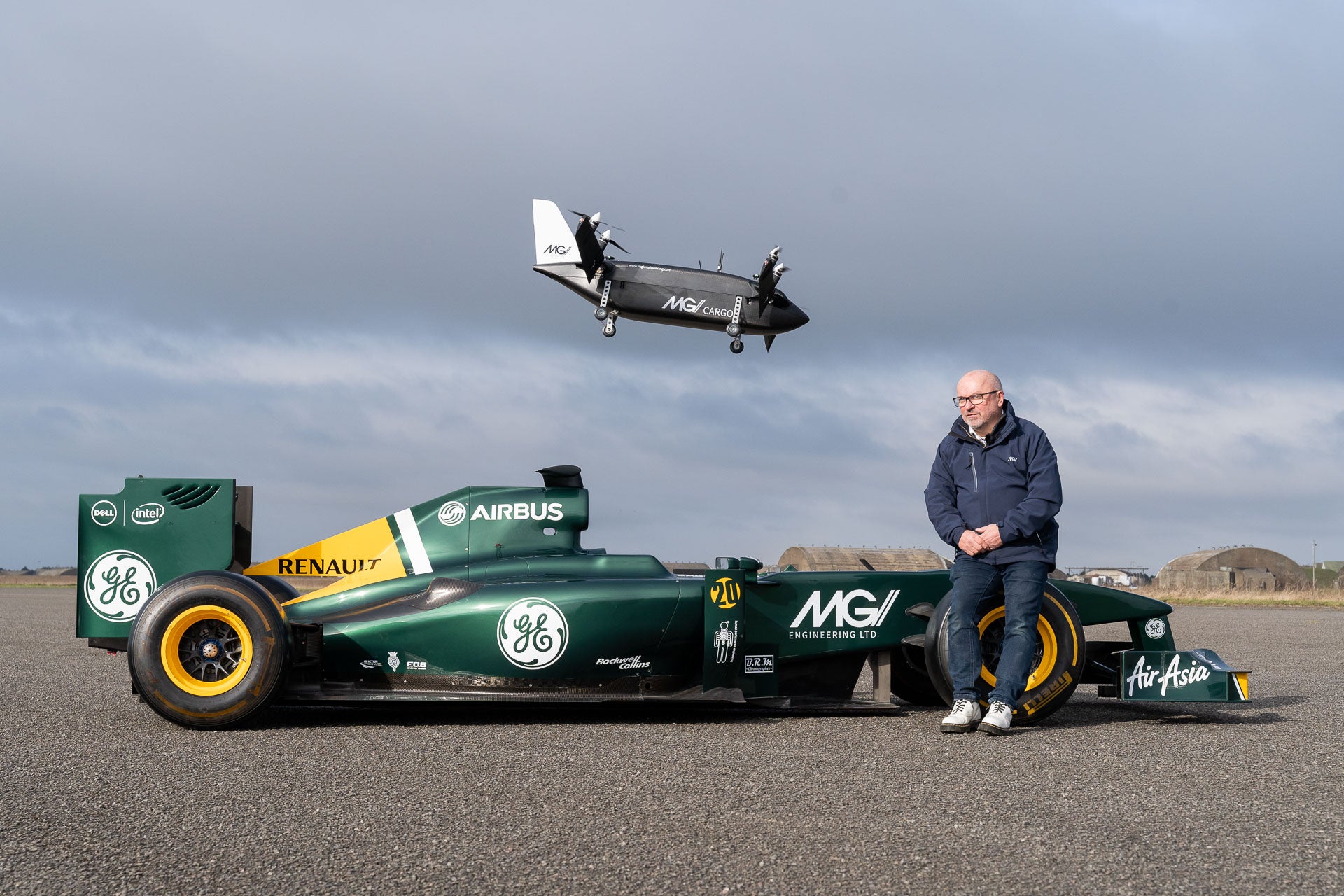
When we think of Formula 1, we tend to associate it with engine noise, the screech of tyres, pointy-nosed and low-slung vehicles, as well as the roar of the crowd. However, you probably don’t think of UAV (uncrewed aerial vehicle) aircraft – but the two have a lot more in common than you might think.
Earlier this year, specialist consultancy company MGI Engineering launched its cargo UAV technology demonstrator programme. Mike Gascoyne, MGI Engineering founder and CEO, showcased the fully functional technology.
MGI is utilising Formula 1 development techniques and experience to create the cargo electric vertical take-off and landing (eVTOL) UAV market. Lightweight composite structures, like those in Formula 1, are being used to provide aerodynamic efficiency for the aircraft.
Frankie Youd spoke to Mike Gascoyne to discuss the design of the eVTOL and highlight the similarities to his previous work in Formula 1.
Frankie Youd (FY): How did MGI Engineering come to be?
Mike Gascoyne (MG): I did 25 years plus at a senior level in Formula 1, rising from being head of aerodynamics at McLaren to being technical director for several teams. MGI was the company I set up in 2003, which I did some consultancy work through and some projects in the background when I was working in Formula 1.
In 2009 I was approached to do the entry into Formula 1 for Lotus Racing, which became the Katrium Formula 1 team. Through MGI, I set up that team, and designed the first car. I stopped working in Formula 1 in about 2015 and started working more full-time at MGI as a consultant.
We initially looked at motorsports and motor racing projects, but what became rapidly very clear was the increasing amount of work that was aerospace-based. MGI came out of Formula 1 principles; if you look at Formula 1 it spends a lot of money developing really clever techniques to save weight, and involves the innovative use of composite materials.
Also, powertrain, suspension systems, cooling systems – a lot of things that are very relevant to the rest of the world. The point of MGI was to bring those techniques and technologies into more mainstream engineering applications.
Although the obvious background is that they’re racing cars, therefore the application would be especially relevant to automotive, a lot of the techniques are actually far more relevant to any lightweight, composite, structured, high-performance vehicle. Modern aerospace, and composite aircraft fit exactly into that – especially the eVTOL aircraft.
When I started working full-time for MGI, that’s how our switch came from being an automotive and motorsport-based consultancy, into a broader-based consultancy and ultimately, almost 100% aerospace-based consultancy.
FY: How have you used your Formula 1 knowledge and applied it to the eVTOL development?
MG: If you want to have a useful, usable range and payload capability, what you need to do is reduce the weight of the aircraft. You need the lightest vehicle you can possibly get.
If you look at Formula 1, and the competition that drives Formula 1, it has driven the use of composites and development techniques to save every last gramme of weight, and that’s exactly the challenge that faces the eVTOL.
In some ways, you’ve got a very obvious and coherent crossover. However, there are problems in that because the Formula 1 world doesn’t have to consider long-life racing cars; parts of racing cars will be discarded after one race or so.
Nothing ages as quickly as a racing car.
They also don’t necessarily have to consider things like corrosion over the lifespan, use in different environments, temperature regimes that vary from very cold to very hot and humid. So, there are a lot of things you’ve got to consider that Formula 1 doesn’t have to.
Of course, then you’ve got to certify whatever you’re doing and prove that it’s safe.
Any new techniques that you want to employ will require efforts to certify them. There are real advantages of looking at the approach from F1, and there are real challenges with doing that as well. But ultimately, if you want to make the lightest possible vehicle, you’ve got to use the latest and most modern techniques, and then get them certified.
You can’t just do what the aerospace industry was doing twenty years ago, because that won’t be good enough. You may be able to certify the aircraft, but will you be able to certify a truly competitive aircraft that can do its targeted range and payload? That’s the real challenge.
FY: Could you discuss the current technology which has been developed by the company so far?
MG: We’ve announced a range of technology demonstrators such as the Mosquito range and we have launched some of the smaller-scale models. These are configurable vehicles. The ones we displayed are capable of carrying 10-20kg. So, small payloads – but these are technology demonstrators, a small-scale model.
The intention is to have a range of larger vehicles which will carry over 100kg. Those vehicles are designed to be configurable, so you can configure the basic chassis of the vehicle, either with rotor only, so with four rotor arms and two motors and propellers on each arm, so it’s a coaxial quadcopter.
Or in the same vehicle, you can put wings on, so front and rear wings, which tilt through 90 degrees. You still retain the ability to take off and land vertically, but with the tilt-wing you could switch to conventional flight.
The Mosquito range is unique in that it’s configurable for both. As technology demonstrators it’s a range of vehicles which demonstrate configurability and scalability.
The larger vehicles use common battery modules so that the same battery modules can be used in different aircraft; we envisage aircraft platforms not being unique to each manufacturer and each vehicle.
We envisage it to be very similar to the automotive model where you have common platforms, some of which are shared between manufacturers, and they then build their own vehicle, or they build multiple types of vehicles on the same platform. We believe that that approach is also where the eVTOL market will go.
FY: Why has the company decided to focus on cargo eVTOL rather than passenger?
MG: The challenges of passenger eVTOL are huge when looking at the safety aspects, and the need to have exceptionally safe vehicles is an additional challenge on top of the other ones I’ve mentioned.
The safety challenges of passenger eVTOL are huge.
We believe that the route into the exploitation of urban air mobility and advanced air mobility and any eVTOL is through the cargo route. Passenger eVTOL will require a huge infrastructure.
I think no one doubts the ultimate impact that advanced air mobility will have and passenger eVTOLs – it’s just how do you get there, and how do you prove that what you’ve done is safe for passengers to fly in?
That’s an additional huge challenge, and we believe the route to the solution of that challenge will be led by the eVTOL cargo market.
FY: What are some of the key benefits of this technology?
MG: It’s green, sustainable, using clean energy, for the first time you have carbon-free aviation, which hasn’t existed until now.
The use of this technology then opens lots of things that weren’t possible before. Helicopters are inherently unreliable and noisy, not green, so the use of aviation in an urban environment for deliveries hasn’t been possible, whereas now it is. These vehicles have the ability to have a lot lower cost per mile and they come with a lot lower maintenance needs.
If you look at applications such as mail deliveries to all the UK islands, delivery of medical supplies, bringing back fresh produce, fish, etc – that doesn’t have to be done by ferries and vans, it can also be done when ferries can’t travel.
That doesn’t require much infrastructure in place other than what’s currently there. Those markets exist currently, I think it’s those markets that we want to target.
This technology can also be used in disaster zones. When the Tonga earthquake happened, planes couldn’t use the runways because of the ash – these aircraft can fly in.
FY: What are the next steps of development?
MG: We’re still a hired consultancy company, so we have other projects. We did one of this year’s current Formula E cars, so we still have our motorsport and top-end automotive work.
We’re looking into funding options and partnership options, because we’d like to develop the smaller version of the Mosquito into a usable product. What’s flying now was always a demonstrator so we will look at designing that in a way that makes it a truly lightweight, usable vehicle with workable payload and range.
It would be very nice when I am retired, to sit in the garden and watch a silent eVTOL fly by and think ‘I helped make that happen’.
Up until now, we’ve been doing that internally; it’s fully funded by MGI, but we’re now looking to work with partners to develop that further, and maybe partner with people on the manufacturing side longer term.
I think, for me, after a long career in Formula 1, this world excites me because it’s using those skills and knowledge that have come out of Formula 1 for something that can really make a difference. As I come to the end of my career, it would be something that’s very worthwhile to look back on having achieved.
Nothing ages as quickly as a racing car. Every year the season finishes, and you essentially throw it in the bin. You can work for 30 years in Formula 1, and you’ll never see anything you designed racing around a track.
It would be very nice when I am retired, to sit in the garden and watch a silent eVTOL fly by and think ‘I helped make that happen’.
This interview was originally published on our sister site, Just Auto.