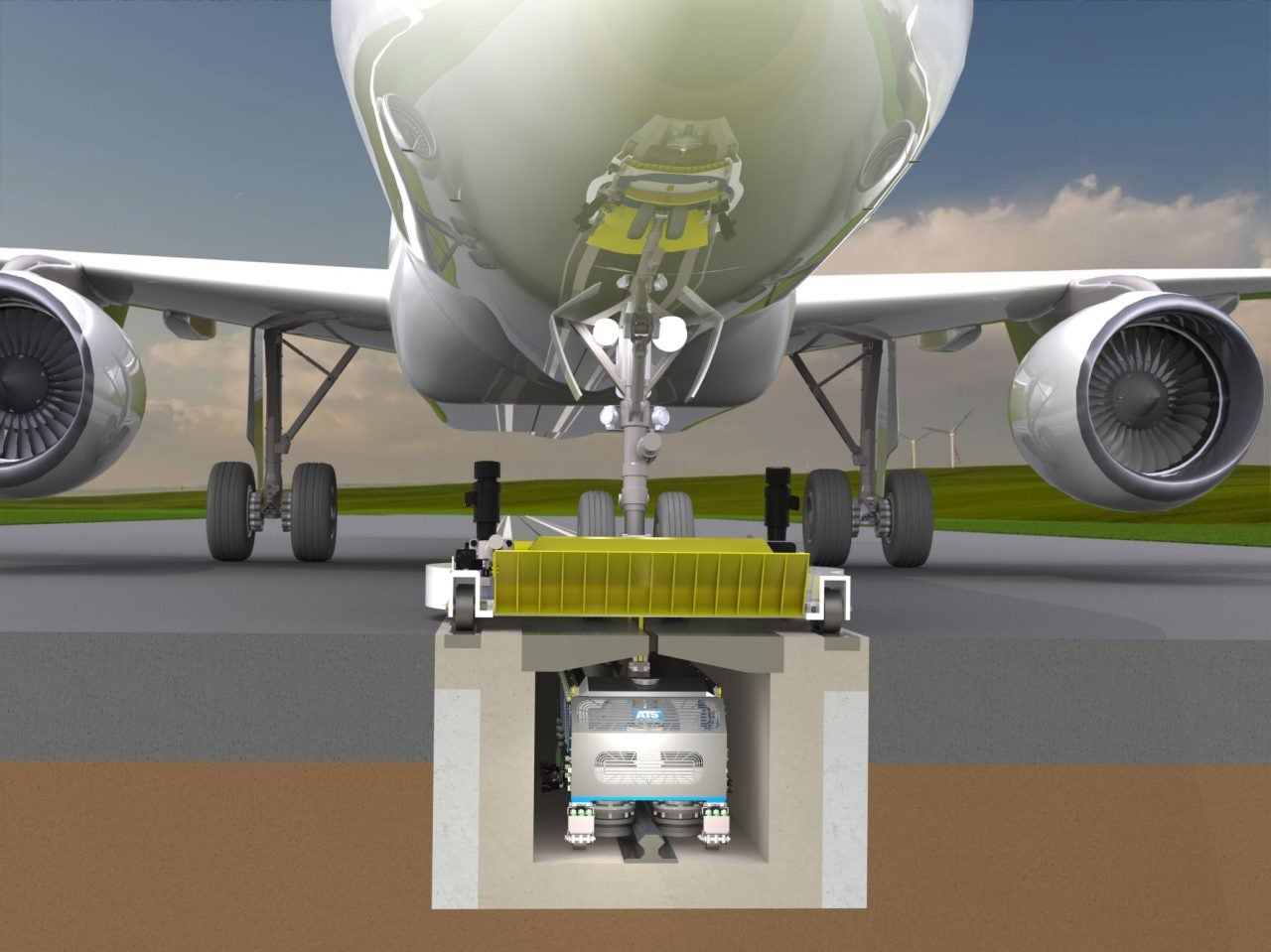
In a recent report published by Shell in collaboration with Deloitte ‘Decarbonizing Aviation: Cleared for Take Off’ stated that in 2019, pre-pandemic, the aviation industry was the source of around 3% of global CO2 emissions. The report also predicted that this number is expected to increase by 22% by 2050.
With these stats in mind, the industry has been working hard to curb its environmental impact by the introduction of sustainable aviation fuel, alternative energy sources and hybrid engines.
Aircraft Towing Systems World Wide LLC have been working on new technology to assist the industry reduce its environmental impact when it comes to ground operations. Upon landing, the new electric powered tow system, developed by ATS, will run along a rail embedded within an underground channel, allowing planes to be towed from the runway to the gates and back.
The technology is hoped to be available for the industry in Autumn 2022.
We speak to Vince Howie, CEO of aircraft towing systems worldwide LLC, to find out more about this new technology and the benefits that it will bring to the industry.

Frankie Youd (FY): Could you provide me with some background on the company and how it aims to assist the aviation industry?
Vince Howie (VH):
In 2016, Aircraft Towing Systems World Wide LLC was established with its headquarters in Edmond, Oklahoma. To bring the concept to reality, that same year Oklahoma State University (OSU) in Stillwater, Oklahoma, was put on contract to perform the design and development work needed to make ATS a functioning system.
ATS created an advanced ground vehicle technology system that has the potential to revolutionize airside operations, specifically, how commercial, military, and general aviation aircraft are moved around airports.
Aircraft are still moved around airports the way they were over 100 years ago – under the aircraft’s power. This old method to move aircraft is very inefficient, burns tremendous amounts of fuel, harms the environment and is dangerous in many situations. The ATS system is fully automatic, utilizing an electric-powered pullcar/tow dolly that rides on a monorail in a below-ground channel and pulls aircraft from the runway to the gate and back.
The safety-enhancing, fuel-saving and environmentally friendly new technology that moves aircraft on the ground will help airports pollute less (either in terms of aircraft and truck fuel consumption, carbon emissions and noise generation) and safer (less collisions and incursions).
Could you explain how the ATS aircraft towing system works?
The ATS system is fully automatic, utilizing an electric-powered pullcar/tow dolly that rides on a monorail in a below-ground channel and pulls aircraft from the runway to the gate and back.
Once the aircraft nose gear is taxied onto the tow dolly, the aircraft engines are shut down and the aircraft rides on the pullcar/tow dolly from the runway to the gate and back.

The benefits of this green and sustainable system are substantial fuel savings, reduced emissions, improved air quality, decreased noise, safer taxiing operations by reducing collisions, higher airport throughput increasing capacity without adding gates, and extended aircraft engine and component life.
ATS would not have been able to develop the technology if it weren’t for advances in electric motor development – their small sizes today can easily be integrated with the underground channel and they are powerful enough to tow aircrafts.
What are the main benefits of using this system over existing ones?
Currently, there are three other taxi systems designed to move aircraft without using aircraft main jet engines to transport aircraft to and from the airport gates.
The first known as ‘TaxiBot’ uses unique battery powered tugs to move aircraft. The other two systems mount electrical motors onto the aircraft nose landing to turn the nose wheels into drive wheels to move the aircraft. This requires modification to the aircraft to install the electric drive motors and gears on the nose wheels.
The electric tug batteries typically have a life of eight hours before needing to recharge. This requires two sets of batteries to operate a single tug for 16 hours of flight operations which are normal in most large airports. It is envisioned autonomous electric tugs would operate in a very similar manner.
The nose wheel drive systems (WheelTug and EGTS) require the pilot to drive the aircraft from the runway to the gate for arrival and for departure from the gate back to the runway. These systems require costly modifications to the aircraft and necessitates additional training for the pilot. They would also require a supplemental type certificate (STC) from the FAA, which would likely be a lengthy process in this instance. The pilot must learn a new operating procedure to drive the wheel tug systems and steer the aircraft.

The ATS solution offers a different method, to replace fuel-burning engine run time during ground movements with renewable energy-sourced below-ground tugs that do not create additional vehicles to track on the airport’s surface. It is an all-weather solution, operating in ice, snow, and rain unlike its competitors.
Could you illustrate the benefits of the system with a case study?
Here is how such technology could benefit an airport like Chicago O’Hare International Airport.
Saving of fuel:
Depending on the type and size of aircraft, fuel usage for one minute of taxiing ranges from five to 18 gallons per minute. Average fuel usage for passenger aircraft at O’Hare is nine gallons per minute while taxiing. Average taxi time is 16-27 minutes. Average number of aircraft movements per year at O’Hare is 800,000.
Nine gallons per minute X 16 minutes taxi time= 144 gallons per taxi X $4.00 cost per gallon = $576 per X 800,000 movements. So, for airliners flying in and out of O’Hare they are looking to benefit over $460 million in fuel savings. This doesn’t take into account the savings associated with airports no longer having to fuel pushback tractors or tugs.
Reduction of emissions:
Taking the fuel savings example one step further, depending on the engines installed on commercial aircraft, the emission output averages 265 kilograms of CO2 per taxi. If you multiply this by 800,000 movements, we’re looking at a reduction of 212 million kilograms of CO2 per year.
A safer airport: The ATS aircraft towing system will help to significantly reduce the number of on the ground collisions or incursions that might occur at O’Hare between aircraft and buildings or vehicles.
Would this be a universal fit, or would additional systems be required?
The ATS aircraft towing system will come in three sizes: large which will accommodate wide body aircraft up to 747 or A380 size aircraft down to regional jets. Medium which will handle 737/A320 size aircraft to regional jets for airports that do not service wide body aircraft, and small for airports only servicing regional jets and/or general aviation business jets.
Based on market demand ATS has devised three configurations to meet airport needs. Each configuration can be combined with one another to create hundreds of variations tailored to meet any airport ground transportation requirements.
Ferry system
A short system to take aircraft from one point to another without the use of aircraft main jet engines. These include de-icing loops, trips to maintenance hangars, trips from one single point to a runway a long distance away.
Pushback option
A system installed at airport gates to replace tugs and towbars. The system will eliminate the harmful emissions emitted by the diesel tugs and never requires fossil fuel. The system is only 100-300 feet long with one pullcar/tow dolly for each gate.
Full airport configuration
A system that includes the pushback feature at every gate and most or all taxiways that have the ATS channel installed. The channel installation is optimized to create the greatest traffic flow and gate optimization to help improve throughput. This system is totally automated with complex integrated software. The complete system provides the greatest return on investment and the largest decrease in emissions and noise with less ground collisions.

What more do you think the industry could/should be doing to reduce its carbon footprint?
The industry has to fundamentally take a hard look at the main causes of increased carbon footprint in the aerospace environment. One way to drive change is to establish far reaching goals such as carbonless taxiing that cannot be met using current technologies. Using thrust to move aircraft is very inefficient, burns tremendous amounts of fuel, harms the environment and is dangerous in many situations.
New disruptive technologies like the aircraft towing system developed by ATS will help airports and airlines meet their carbonless taxing goals.