
Narrow-body aircraft such as the Airbus A320 and Boeing 737 can accumulate more than 300kg in extra humidity weight during a flight. Keeping the weight low can save more than 20 tonnes of fuel annually, which equates to 66 tonnes of CO2 emissions. This could be even more in wide-body aircraft like the Boeing 747 and Airbus A380, which can accumulate more than 500kg.
The outside air temperature at 30,000 ft is -50°C. Despite the cabin air being dry, the cold fuselage causes humidity from passengers’ breath to condensate on areas without insulation or gaps.
The condensation forms into water drops that drip into insulation blankets until dried. In a cabin that is significantly full in a cold climate, the situation can become so severe that condensation has been seen dripping from the overheads onto passengers.
Dehumidification solutions and how they work
CTT Systems’ Anti-Condensation solution includes a fan, a slow-rotating adsorption rotor with a heater. The fan directs air through the intake and the rotor dries 75% of the air while the other 25% is heated to release the adsorbed moisture. The released moisture is trapped and disposed of or recycled and the dry air is fed up into the crown area through piccolo ducts.

The area where the humidity and water was is then dried out. Eventually, the insulation blankets will dry out, which can take between four to six months. The aircraft is 250kg lighter than it would have been without this process, saving fuel and reducing CO2 emissions.
How well do you really know your competitors?
Access the most comprehensive Company Profiles on the market, powered by GlobalData. Save hours of research. Gain competitive edge.
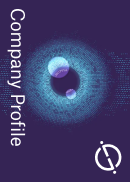
Thank you!
Your download email will arrive shortly
Not ready to buy yet? Download a free sample
We are confident about the unique quality of our Company Profiles. However, we want you to make the most beneficial decision for your business, so we offer a free sample that you can download by submitting the below form
By GlobalDataCTT Systems director of sales and marketing Ola Häggfeldt says: “It is a solution we developed some 20 years ago. It originally came from Saab’s military side and was first used in a commercial application on Saab 340 aircraft where they had condensation problems. This solution was adopted to be more generally fitted on various aircraft types and over the years it has evolved.
“We have improved the rotor to have high efficiency and the heating system has improved over the years as well as the fan which provides air over the rotor. It is an evolution of that solution to increase capacity and efficiency. It is also tailored to as many aircraft as possible.”
European airlines including Transavia, Jet2.com and Pobeda have used the system in their fleets. Overall, around 3,500 systems have been installed. However, an increasing number of low-cost airlines and those with high-density configuration aircraft are expressing a renewed interest.
The system is particularly beneficial for narrow-body aircraft, except on desert routes where the sun would naturally provide the same benefits.
Häggfeldt explains: “Today, many commercial aircraft have retrofitted systems, especially the aircraft which fly in the northern hemisphere because the problem you have with the condensation and the building up of moisture and water in the insulation blanket is more when you are in cold climates than when based in a desert-like environment.”
While benefits include drying out areas of the aircraft and reducing fuel consumption, it is also possible to make significant cost savings.
CTT Systems are not alone in this market; developers such as the UK-based Munters and Sweden-based Salmek are also key players in aircraft dehumidification. Salmek’s dehumidifier uses a stationary absorbing core which can save up to 35% energy and the use of a built-in heater increases evaporation.
Cost-saving solution: the appeal of dehumidification
The cost of the system depends on the number of passengers the aircraft is configured for but can offer a short payback time. Aircraft last 20- 30 years so the ability to pay back in one year or a year and a half is considered a good saving. In addition, production costs can be reduced as the volume increases.
“If the volume increases, production costs of the system can be reduced but the benefit is mainly on oil prices and emission rights. The cost of fuel and emissions has gone up,” says Häggfeldt
The system has low energy needs, mainly for the heater, and while the solution adds 25kg to the weight of an aircraft, it removes 300kg of water weight during a flight.
In addition, using the solution to remove water from areas where electronic equipment is fitted on the aircraft can reduce maintenance costs. Electronic equipment is especially sensitive to water around it when it freezes.
Reduced humidity in the areas between the cabin lining and the fuselage reduces the amount of maintenance required for electronic equipment. The resultant savings are even greater than those from fuel consumption.
Salmek has published a report, Use of Dehumidification to Reduce Preventive and Corrective Maintenance of Aircraft Due to Corrosion, focussing on fighter aircraft. It reinforces the importance of using dehumidification to protect aircraft as many have electronic equipment which can be sensitive to humidity, pressure and changes in temperature.
Future focus
While a dehumidifier system works well for high-density narrow-body aircraft and short-haul flights of two to three hours, wide-body aircraft on long haul-flights that of six hours also require a humidifier to balance over-dry air.
CTT Systems has a segment of the business focused on humidification, as the pilot’s area, crew area, business class and first class are extremely dry. CTT Systems’ solution brings the humidity up to 22% from 3% to 5% to prevent dry skin, dry eyes, discomfort and dryness-induced fatigue.
The extreme dryness in those areas of the aircraft can affect the immune system, mucus membranes and respiratory system during long haul flights.
“With the pandemic going on, this has become higher on the agenda as diseases spread much more like in the winter in dry air,” notes Häggfeldt.
“In a long-haul aircraft without humidification, from a humidity point of view, it is better to sit in economy class. The aircraft has a HEPA filter, so the regenerated air is clean from the ventilation system but the moisture in the aircraft is generated by the passengers.
“The 787 was the first aircraft to have humidification for the flight deck and somewhere between 85% to 90% of aircraft now have this. Today it is also available for the flight deck, crew rest and cabin on A350 XWB and the coming 777X.”
While a significant number of aircraft have integrated this solution, CTT Systems expects to obtain a certificate for the 737 Max, the only aircraft for which the company does not have a certificate because it is currently grounded.