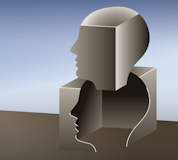
Airport supply chains are complex beasts. Not only is it essential for inbound and outbound cargo to flow smoothly through the system, this process also needs to be choreographed to ensure that it does not negatively affect passenger flows or airline timetables; however, speed is not the only factor that airline operators need to consider. An ever-growing catalogue of customs regulations means that many facilities have fallen into the trap of implementing a host of time-consuming cargo checks in order to meet the stringent security criteria set out by industry legislators.
But there is a more efficient solution, as Amsterdam Airport Schiphol (AAS) has demonstrated with its SmartGate Cargo initiative, an innovative and, importantly, collaborative system that aims to improve the speed, safety and reliability of cargo transactions.
Built around the first international collaboration of its kind between the private sector and government agencies – namely AAS, Air Cargo Netherlands (ACN) and Dutch Customs – SmartGate Cargo was born out of a wish by all three bodies to improve current cargo monitoring systems and create a robust logistics process for imports and exports at AAS.
"The goals behind the project were to ensure that Schiphol is the quickest airport in terms of imports-exports, and the simplest in the predictability of processes," says Enno Osinga, senior vice-president of cargo at AAS. "At the same time, we designed the processes to make sure they are capable of dealing with change and new regulations. The world is changing so fast that I hope the project will never be ‘ready’; it will continuously be adapting to new requirements."
What is SmartGate Cargo?
SmartGate Cargo is a one-stop-shop for cargo monitoring, which means that every party involved in cargo transactions only has to deal with a single inspection system, allowing efficient clearance of cargo.
"There were a lot of opportunities to smooth the whole process, reduce waiting times and create transparency so everyone who needs to see a particular aspect of the process can see it," Osinga explains. He stresses that it is essential that SmartGate Cargo is not one single process; rather, it’s a wide-ranging project encompassing a large number of processes and technologies – from scanning equipment to the control centre.
"The first thing we did was related to physical scanning equipment," Osinga says.
"We needed to make sure that the scanning equipment was available so that everything that had to be made visible was made visible, as well as deciding where in the process this could be most easily implemented and how it works in practice."
Secondly, the project leaders introduced the E-Link system. The existing ACN pass that all drivers require to offload cargo at AAS has been expanded into a ‘smartcard’, reducing the amount of paperwork the driver has to carry around. Now, the driver can load all the necessary information regarding his customs-cleared shipments onto the card and enter the facility almost immediately, thanks to number-plate recognition and identification through the ACN pass. Responsibility for the shipment is then transferred to the next link in the supply chain and the driver is automatically assigned a door to offload his cargo.
"At that moment, customs know the driver’s material has arrived at the handling point and can begin planning inspections," Osinga explains. "We’ve brought that stage much earlier in the process and because of the reduction in paperwork, the process is now much simpler."
The customs control centre is perhaps the most important piece in the SmartGate Cargo system, as it is the place where all the information – from drivers, handling agents and airlines – comes together. "Based on this information, customs can then identify which shipments they need to inspect and start planning the process," Osinga says.
As the system develops, customs also plans to build a central scanning facility.
"There will be scanning equipment with the different handling agents, which is connected to the customs control centre," says Osinga. "So, although the goods are physically scanned with the handling company, customs will have the overall supervision and make decisions based on the results of the scans.
We have different pieces of technology all over the airport, which all link to create one collective SmartGate and this is another reason why the project will never be ‘ready’; the technology is developing on a daily basis."
The final piece of the puzzle is the Information Broker system, developed by Cargonaut, which allows the aviation sector and government agencies to determine whether a shipment will require inspection at AAS in advance on the basis of electronic pre-departure and pre-arrival information.
"Forwarders can deliver all the information regarding goods into one database, which customs can access at the customs control centre," says Osinga. "Then, when the shipment arrives and goes through the E-Link system, they can actively take whatever action is necessary."
A work in progress
The Smartgate Cargo concept was introduced three years ago, but organisers are taking the project one step at a time. The customs control centre and the Information Broker have been operating for a year, while the scanning pilot has been in place for 18 months. E-Link was implemented recently, and the project leaders expect the first phase of SmartGate Cargo to be up and running by late 2015. Yet, there are no statistics to demonstrate how successful the project has been.
"We’re not focused on the figures," says Osinga. "We know we want to improve the process and we know that the various processes we’re implementing are speeding up the process, but we haven’t sat down and measured, say, how many minutes each truck driver saves thanks to E-Link. Similarly, we don’t have a single budget for the project. The SmartGate Cargo system is trying to coordinate all the organisations involved into developing their own products in such a way that they all match and meet but have their own individual budgets. For us, it’s really about what we’re going to do together for the future."
However, there are still several challenges to overcome before the collaborators’ vision can be fully realised.
"The main challenge is to get everyone in the supply chain working in the same direction," Osinga explains. "Moreover, it’s difficult to get people in the logistics industry, which is a very marginal business, to invest in something that they might not see the benefits of for two or three years."
On top of this, it often transpires that party A needs to invest in one particular technology, but the benefit of this investment will go to party B.
"You need to get that aligned," Osinga says, adding that it is similarly difficult to ensure that all the different government processes and inspection agencies are aligned to work together and exchange information, particularly in the face of evolving security regulations.
"Managing change takes time," he adds.
Although the logistics industry has not traditionally been fond of change, the SmartGate Cargo team is doing everything it can to get the next generation of employees inspired to embrace innovation. They’ve even come up with ‘SmartGate: The Game’, which shows players how the supply chain works and illustrates the advantages of using SmartGate Cargo.
"It’s a fun way of getting young people involved in the industry," says Osinga. "It opens up the system to the people in the market and shows them what these changes could potentially mean for the industry.