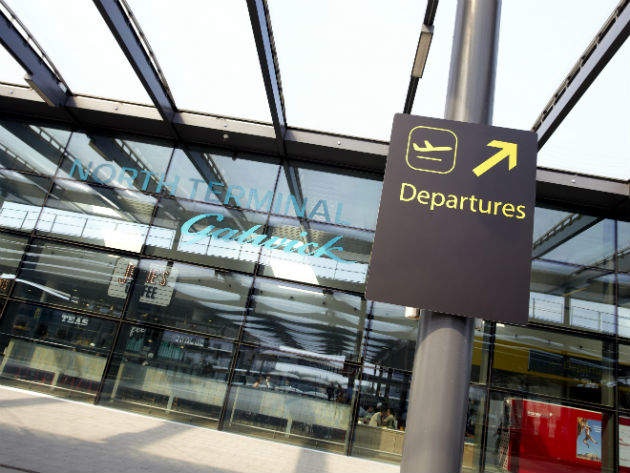
The environmental discussion around aviation tends to focus on the planes themselves. Though still a significant emitter of emissions, better engines and advances in aerodynamics mean that modern aircraft are considerably quieter, more fuel-efficient and less polluting than they were only 10 years ago.
What is often overlooked, however, is the waste produced by airports, which today function as cargo and transit hubs, maintenance centres, shopping malls, restaurants and offices – all rolled into one. According to data from the Civil Aviation Authority, in 2013 the UK’s largest airport Heathrow produced 26,693 tonnes of waste, equivalent to 0.37kg per passenger; and that’s factoring in a comprehensive recycling system that saw only 5.9% of waste go to landfill.
The situation has been made more difficult by the restrictions on liquids introduced in 2006. According to an August article by the Bristol Evening Post, passengers at Bristol Airport leave nearly 1,000 bottles of liquid a day at airport security after being told they can’t take them on the plane.
Airport environment especially challenging
Waste disposal is particularly tricky in the airport environment. Hundreds of waste streams are scattered throughout the complex, and bringing them together is made difficult by the need to maintain access restrictions and strict rules governing the separation of different types of waste. Category 1 waste, the most hazardous grade of animal by-products, is especially problematic for airports.
Listed under this category, along with horrifically dangerous things like disease-infected wild animal carcasses and carcasses of animals used in experiments, you find international catering waste. This is defined as food waste and anything mixed with it, such as cups, trays and packaging, from international transport vehicles. In actuality, this means any aircraft or ship from outside the European Union.
While it may seem strange to find leftover airline food in the same category as rotten lion carcasses, this categorisation makes perfect sense given the ease with which diseases such as foot and mouth can be transmitted across borders. But it means that up to now, airports in the UK have had to process all Category 1 waste offsite to protect against any outbreaks, which adds logistic complexity and expense to the waste disposal process.
Gatwick trying something new
Gatwick Airport has become the first to buck this trend. In November it announced the start-up of a £3.8m waste processing plant, which will make it the first airport in the world with the ability to legally dispose of Category 1 waste on site. In addition, Category 1 and other types of organic waste are to be turned into biomass fuel to power the processing plant and provide heating for the North Terminal. The project is being managed by the airport’s waste handling contractors DHL, with food waste technology specialists Tidy Planet providing the biomass combustion and preparation systems.
“In terms of recycling, like many organisations, we found that our rates plateaued and we struggled to move the needle above the 50% mark,” says Simon Duggan, senior logistics & waste manager at Gatwick Airport. “The strategy drove us to constantly look at how we can improve our targets and in partnership with our new waste handling contractors DHL – a company that has extensive experience in this area – we devised this project. When the scheme is fully up and running we expect our recycling rates to jump to 60% in 2017, 70% in 2018 and then up to 85% in its fifth full year of operation.”
Under the new system, dry mixed recycling and general waste from the airport is taken to a materials recovery facility where it is sorted. Then waste that can’t be recycled is sent to a dryer where it is turned into pellets to be used as biomass fuel. Category 1 waste skips the materials recovery step and goes straight to the dryer. The resultant pellets are put into a biomass boiler, which generates 1MW of renewable energy. Water recovered from the drying process is used to clean airport bins, while ash from the boiler goes into the production of low-carbon concrete.
Duggan doesn’t go into specifics about how the project has managed to stay within the rules that govern waste separation, but emphasises the importance of working in step with regulatory authorities.
“The rules remain very strict and that is where the innovation for this scheme lies,” says Duggan. “We have found a way to comply with the strict regulations by working very closely with Defra and the Animal Plant Health Authority to ensure that the technology and our processing system meet their requirements. That has been the real challenge behind making this project work.”
Fusing people with technology
Now the plant has started up, the main priority is to create a waste disposal procedure that allows all 130 on-site businesses to partake without having to make considerable process changes or carry out extensive retraining. This is helped by the fact that each business doesn’t have to separate its own recycling. “We do the waste sortation for them [on-site businesses] at our end, which is one way we manage to generate such high recycling rates – by bringing responsibility for sorting in-house,” Duggan says.
Then it’s all about ensuring the facility can keep pace with the rapid growth of air travel that we are seeing throughout the world. Last year was the busiest in Gatwick’s history, with 40.8 million passengers passing through, an annual increase of 5.5%. The airport currently treats 2,200 tonnes of Category 1 waste each year – around 20% of the total generated at the airport – and the new plant will process approximately 10 tonnes per day. Duggan’s team is already looking to scale up in line with this.
“We are currently looking at adding capacity to cope with around 45 million [passengers] a year, up from almost 42 million this year,” he says.