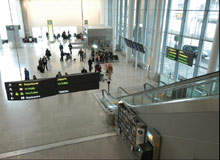
Toronto Pearson International Airport (TPIA) has undergone massive growth over the last decade to become Canada’s busiest airport. The development has involved huge investment in infrastructure and resources, which is ongoing.
The rapid acquisition of new assets complicates the issue of asset management. The Greater Toronto Airports Authority (GTAA) has invested in a comprehensive asset management system, which it has integrated with the overall airport development, in the hope that good preparation will forestall potential problems as these assets get older.
RAPID GROWTH
From its modest beginnings in 1938 as Malton Airport, TPIA has become Canada’s main airport. Business, personal and leisure travellers, as well as air cargo shippers, use it to access air services to over 300 destinations worldwide. TPIA is an important economic asset in the greater Toronto area and a vital component of the regional economy.
In 1994, the government of Canada transferred the management, operation and maintenance of 26 airports to locally controlled Canadian airport authorities. The GTAA was incorporated in 1993 and took control of TPIA on 2 December 1996. Its mandate includes the operation and development of TPIA.
The GTAA has proceeded expeditiously with a number of projects to meet its mandate. In 2005, TPIA was the 29th busiest airport in the world, with a total throughput of just under 30 million passengers.
TPIA DEVELOPMENT PROGRAMME
Since 1998, the GTAA has managed a CAN$4.5bn airport redevelopment programme to prepare for the 50 million passengers expected by 2020. All aspects of the airport have been improved:
- Two new runways, new taxiways and provision for a future sixth runway
- New Terminal 1 (four million square feet)
- Demolition of old Terminal 1 (completed)
- Demolition of Terminal 2 (2007)
- Terminal 3 capacity expanded by 40%
- New infield development (hangars, food preparation and cargo)
- New central de-icing facility (the world’s largest)
- New glycol recycling plant
- New storm water facilities
- New south development (service buildings, administration)
- Rebuilt highway 409 and access roads into Pearson
- New central utilities plant
- New 117MW cogeneration plant
- Most electrical, communications and other utility systems rebuilt on campus
With an approximate total value of CAN$6.2bn, the challenge is how to maintain these assets for their full lifecycles. Because most of the facilities are new, the GTAA has a few years before significant asset lifecycle expenditures will be required. However, it is already preparing its asset management systems.
MAINTAINING GROWTH
A facilities asset management system (FAMS) tracks data on assets, grouped by class (building, structure, pavement, infrastructure), and uses age and theoretical life to predict a lifecycle for each major technical component. Most importantly, it generates an inspection event for technical components well in advance of their predicted failure.
In 2002, the GTAA decided to use the RECAPP asset management system developed by Physical Planning Technologies Inc of Richmond Hill, Ontario.
The system identifies potential long-term funding for capital asset repair or replacement at least 20 years ahead. Following condition assessments six years before anticipated lifecycle issues, events are moved into a tactical planning window for the next five-year period for prioritisation and more detailed capital allocation. Finally, the results of the more detailed work moves into an approved capital plan for the current budget year.
The system provides information on the technical details of each asset. For example, for runway 05/23, data on pavement structure, drainage systems, lighting systems and pavement markings are provided (see figure 1). This aids lifecycle management as technical data with similar physical characteristics and lifespans are grouped together.
Each technical datum has two potential events that may recur several times: inspect and replace. A replace event coincides with the end of each component’s theoretical life. The first inspect event, which includes a condition assessment, occurs six years before the replace event to provide data for the capital planning process.
For each replace event, the inspect event answers four questions:
Validity: do we really have to do this?
Scope: how much work is involved?
Schedule: is six years from now the best time to do it?
Budget: how much will it cost us?
Following the results of the inspections, the system then moves the projects either into a five-year tactical window or defers them if possible.
In addition to RECAPP’s built-in asset validation system (AVS) for buildings and structures, condition assessments are carried out using a variety of tools that have been developed externally for specific applications.
Certain assets, such as electrical and communication ductbanks, are inspected and reported in-house. These assessments provide information about the condition of each asset, allowing decisions about the extent and timing of repair or replacement. The RECAPP data manager assembles all this information into a comprehensive reporting and analysis tool.
The database also provides information on four asset classes for capital planning and accounting purposes: buildings (terminals, cargo, offices and maintenance), structures (bridges, tunnels and parking garages), pavements and infrastructure. As much as possible, GTAA uses its own construction cost data to form the basis of model estimates.
Where the information is not readily available, RECAPP uses external data sets, such as MS Means, which are adapted to reflect the premiums required for a live airport environment. Forecasts are made in current dollars and adjusted at least annually for inflation and construction cost-cycle changes so the current capital programme budget numbers are up-to-date and five-year forecasts are always relative.
It is also possible to model different scenarios of fund application to allow better-informed decisions under limited funding conditions. For example, what would be the physical and financial impacts of deferring CAN$1m worth of apron repair for a year to address an immediate need for improvement or to develop a significant business opportunity?
It is important to distinguish FAMS, a capital planning tool, from day-to-day maintenance planning tools. GTAA uses its airport maintenance management system (AMMS) to manage the routine, ongoing expense maintenance. Though the two are related, FAMS is a strategic tool while AMMS is operational.
FAMS IMPLEMENTATION
Implementation of FAMS started in late 2002. Because of the huge amounts of information involved, gathering the data and organising and entering it into the system is a time-consuming project. Existing assets were assessed first because their lifecycle restoration events will be required earlier. In many cases, this has meant initiating condition surveys that had never been formally done for long-range FAMS purposes; the work continues.
Data on new assets are being integrated as the assets are built and put into service. One engineering staff member is dedicated full-time to the FAMS effort, assisted by an engineering student year-round. He heads a FAMS committee made up of
representatives of operations, facilities, engineering and finance, which meets at least quarterly.
At the start of each capital programme budget cycle, FAMS information on all projects in the current five-year-plus windows is reviewed by a GTAA management committee. Current-year FAMS projects are individually identified in the overall capital programme and projects within the five-year tactical window are aggregated into the four accounting categories.
This is to underline the fact that the scope and timing of many of the projects will be adjusted in the five-year period, and other projects will be inserted into the overall capital programme. Hence, for ease of administration, the FAMS projects are treated as separate mini capital programmes.
Capital expenditures are required to satisfy a number of mandates:
- Legislative requirements
- Safety and security improvement
- Environmental improvement
- Executive mandate
- Operational necessity
- Customer service improvement
- Lifecycle upkeep
- Business opportunity
Thus, lifecycle/FAMS events must always compete with other issues for capital, and it is important that all of these drivers can be adequately addressed and properly prioritised. The capital programme involves rigorous priority setting based on ten criteria.
These apply to all projects, of all disciplines and regardless of the source of the expressed need for the work. Each project must stand on its own merits. Mission-critical FAMS projects are appropriately placed once timing issues are confirmed from an engineering and operational perspective.
FAMS will ensure that the GTAA derives the greatest possible benefit from its assets and capital spending by identifying the need every year for certain critical condition assessments to validate the timing and scope of lifecycle events. This helps avoid reactive or surprise repairs and their associated cost and operational implications.
It also provides clear links between facility asset management planning and capital programme management. It does this in such a way that all constituents and stakeholders in the airport are kept well informed of future funding and operational requirements for asset management purposes.