
For Oslo Airport, Gardermoen (OSL), Norway's principal airport since 1998, the winter season starts on 15 October and finishes on 15 April. The airport is located inland, just north-east of the capital city, and its two million square metres of runways, taxiways, exit ways and aprons are subject to harsh weather during the cold season.
Although conditions can be crisp, sunny and bright, snow and rain are never far away. "In October and November the temperature is normally about 0°C, with the first snow tending to fall in November," says director, airport services Erik Gill.
"Initially it can be a mixture of snow and rain but, if the ground temperature is below zero when the rain falls, it freezes to ice on the surface. It gets a little colder in December and there is normally a lot of snow in January, February and March."
The worst period of snowfall was in winter 2002-03, when the airport saw a total of 2.7m. In December and January there is also a long period when freezing fog and drizzle cause problems, says Gill. This can lead to difficulties with ice build-up on aircraft engines and runways, where it can cause braking problems.
First defence
The first line of defence against the winter weather is an arsenal of snow sweepers, blowers and ploughs. "When it begins to snow we start up the machines; cars with scrapers in front and sweepers, plus blowers to move the snow away," says Gill.
How well do you really know your competitors?
Access the most comprehensive Company Profiles on the market, powered by GlobalData. Save hours of research. Gain competitive edge.
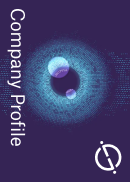
Thank you!
Your download email will arrive shortly
Not ready to buy yet? Download a free sample
We are confident about the unique quality of our Company Profiles. However, we want you to make the most beneficial decision for your business, so we offer a free sample that you can download by submitting the below form
By GlobalDataThe next step is chemical removal. Civil aviation regulations stipulate that black runways should be kept as clear as possible, so OSL uses formate (a salt of formic acid) to remove the last layer of ice.
"There are restrictions regarding the use of chemicals," says Gill. The airport is unable to use the quantities of chemicals it would like because it is not allowed to pollute the groundwater. The combination of formate and glycol, which is used to de-ice the aircraft, easily gets through the earth into the groundwater. Because of the risk of polluting the water table, Gill's team also uses large quantities of sand to help keep the runways clear.
Winter workers
Gill employs a core maintenance team throughout the year, which operates in five shifts, led by a duty supervisor. The airport takes on about 130 additional temporary staff each winter.
"Many of these employees return annually but some will be new, so between the end of September and beginning of October we run training courses covering communications, how to handle the equipment, and the processes involving sand and chemicals on the runway. The more experienced personnel go on refresher courses and for new staff we have a more comprehensive training programme."
The winter operations team needs to have access to the latest weather information, as it is essential to start preventative measures and clearance as soon as possible.
The team has regular communications with the Norwegian Meteorological Institute, as well as using its own weather radar and temperature-detection systems on the runway.
Snow-removal procedures have been established over a period of ten years and follow a precise set pattern.
One team takes a runway while another deals with the taxiways, both teams clear the crossways, then everyone moves to the next runway, repeats the process and returns to the first runway to start the cycle again. Plane de-icing is done by the handling companies in a designated area.
"The whole process, from leaving the first runway clear to returning to start again, takes an hour," says Gill. It takes 15 minutes for the runway to be cleared, treated with chemicals and subjected to friction tests for braking values. The procedure continues for as long as the snow falls.
"Members of the team continuously monitor the friction along the runway, and sometimes on the apron and the taxiway, both by measurement and visually," says Gill. "The measurements are then put into a computer in the car. They go directly to a centre in western Norway and then back to the tower at the airport."
Snow blowing
The team has an excellent record of keeping the runways open during the winter. There had not been a single closure until February 2008.
"The big blowers are some of the most crucial pieces of equipment during the winter because of the amount of snow we need to clear," says Gill. "On 1 February 2008, when two of the big blowers were sidelined for repairs, we had an almost unprecedented snowfall," he recalls. "About 15cm of wet, heavy snow fell in the space of two hours. We couldn't keep the friction levels high enough, so we were forced to close.
"Unfortunately a KLM 737 overran the runway and this, together with the continual snow, meant that the runways were closed for five hours. Normally with that level of snow, the airport would have reopened within two hours." The airport now has two extra snowblowers.
Gill has seen some big changes in his time working at Gardermoen. The chemicals used to remove the ice are much improved today, plus the winter team is better educated and trained, and more able to solve problems as they arise, he says. Snow-removing equipment is also constantly improving.
Climate change is also making an impact. "In the past two seasons we have noticed that climate change has made it even more difficult for us to maintain satisfactory conditions on the runway, because the variation in temperature is moving between 2°C and -4°C. The temperature rises above zero and the snow melts, yet we still have below-zero temperatures in the ground, which causes problems with ice build-up."
Another challenge involves sand. "We are using a bit too much sand on the runway, which is bad for the aircraft engines and undercarriages," says Gill. "Airlines are unhappy about the amount being used so the team is reassessing the use of sand and researching whether the chemicals could be used more effectively."
Gill is determined to reduce the time taken to complete the procedure even further. "We are getting more equipment and reassessing all our processes," says Gill. "It is a tough challenge because air traffic is increasing and the time between each aircraft movement is reducing. But I believe we can improve our service even more."