The innovative application of key materials has long been pivotal in the development of new technologies. However, the impact of materials science and its broader market is often overshadowed by the platforms and advanced tech capabilities such as quantum computing and AI within the aerospace and defence sectors, despite its outsized impact on capability modernisation over the past several decades.
How a material has been processed determines how it can be used – the physical and mechanical properties of a material, as well as its expected service life are all a result of how it has been processed – so an understanding of materials processing is essential in the design of high specification engineering components.
Metals: The fastest air-breathing manned aircraft to have ever existed, the Lockheed Martin SR-71 Blackbird, owes much of its place in the history books to the role played by the advanced materials (AdMs) in its construction. Titanium, a very cutting-edge material in the mid-20th century which previously had very limited applications, was used to construct 93% of the SR-71’s aerostructure due to several innate benefits. Titanium alloys can provide a unique combination of strength, lightness and thermal resilience which is unmatched by materials such as steel or aluminium. Heat resistance was of particular importance in the development of the SR-71, given its target cruising speed of Mach 3+. At hypersonic speeds, aerodynamic heating – heating of a solid body produced by its high-speed passage through air – requires not only significant heat dissipation but also a resistance to thermal expansion. Titanium was, therefore, an ideal material for this application, as it has thermal and tensile strength properties similar to most steels while being 50% lighter. Since the retirement of the SR-71 in 1999, titanium alloys haven’t seen use as extensive as in the SR-71, but instead, development has focused on optimising alloy compositions for specific applications. The Airbus A380 uses titanium in many places where other materials would not be sufficient. For example, pure titanium has replaced many elements of the airframe where steel was previously used, due to its comparable strength and significantly smaller weight. This has only been possible due to the precipitous drop in the price of titanium over the last 50 years. The A380 also employs several titanium alloys for some high-temperature (600°C) components in the fan and compressor in the front of the engine, for similar reasons as their use in the SR-71.
Alloys: In the second half of the 20th century, many of the material improvements centred around the adaptation of widely used metals (i.e. steel, aluminium and nickel) into alloys through the addition of other elements, thereby adapting their microstructures and enhancing their macroscopic properties. In the simplest cases, this involved basic alloy compositions, such as the addition of lithium to aluminium, reducing aluminium’s weight without significantly affecting strength. However, it is possible to engineer alloys of more complex composition to produce a far greater benefit. For example, the development of nickel alloys and superalloys, usually containing a combination of nickel, aluminium and titanium, significantly diversified nickel’s applications by enhancing its maximum working temperature. Alloying nickel facilitates its use in temperatures greater than 70% of its melting temperature as a result of both the exceptional oxidation and creep resistance – time-dependent deformation of a material under constant stress – afforded by the alloying elements. The widespread use of nickel alloys in turbine blades and engine components enabled far greater operating temperatures, greatly improving the fuel efficiency of modern jet engines, which operate most optimally at higher temperatures. However, nickel superalloys remain incapable of reaching the most optimal combustion chamber temperature of 1,700°C, thus research in this field continues as experts seek to develop thermal barrier coatings capable of withstanding those extreme temperatures.
Composites: Composite materials are becoming an increasingly prevalent form of AdMs and are being used in a growing multitude of commercial and military applications. One of the most striking examples in recent years is Boeing’s 787 Dreamliner aircraft, with 80% of its airframe’s volume being comprised of composites (50% by weight) such as carbon or glass fibre-reinforced polymers (FRP) within different structural architectures (fibres, laminates and sandwiches). This provides several structural benefits such as improved strength and reduced weight compared with aluminium alloys-based airframes, as FRPs are 2-5 times stronger and 50% lighter equivalent aluminium alloys. The resulting benefits include improved fuel efficiency by a factor of 20%, increased maximum range and reduced necessary maintenance as a result of the greater design simplicity afforded by composite architectures. The fatigue behaviour – or initiation and propagation of cracks in a material due to cyclic loading – of composites is also superior to that of common industrial metals such as aluminium, steel and titanium, consequently making composites ideal materials for aircraft fuselage which are subjected to stress in cyclic loading throughout their lifetimes as a result of cabin pressurisation and depressurisation.
Overall, it’s safe to say that the development of new and cutting-edge advanced materials has always been inextricably linked to innovations within the aerospace and defence industries, and though procurement priorities continue to shift the overarching importance of materials science will likely remain undiminished. In addition to further enhancements in composites and alloys, nanotechnologies, metamaterials, and energy storage and generation materials all look to be set to disrupt the engineering status quo over the coming decades and facilitate the development of truly transformative capabilities within the aerospace and defence sectors.
How well do you really know your competitors?
Access the most comprehensive Company Profiles on the market, powered by GlobalData. Save hours of research. Gain competitive edge.
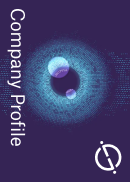
Thank you!
Your download email will arrive shortly
Not ready to buy yet? Download a free sample
We are confident about the unique quality of our Company Profiles. However, we want you to make the most beneficial decision for your business, so we offer a free sample that you can download by submitting the below form
By GlobalData
Related Company Profiles
Airbus SE