
A new case study by a team from Northwestern University in the US has confirmed that 3D printed metal parts will help reduce weight of an aircraft by up to 7%, thereby allowing airlines to save fuel and decrease carbon emissions.
Backed by the US Department of Energy’s Advanced Manufacturing Office, the case study used aircraft industry data to evaluate lifecycle environmental effects of using 3D printing for metal aircraft parts.
The lighter and higher performance parts that are produced using 3D printing technology will also help reduce manufacturing waste, the team said.
Northwestern McCormick School of Engineering materials and manufacturing Morris E Fine junior professor Eric Masanet said: "The airline industry is an early adopter of 3D printing.
"The main driver is that aircraft require specialised lightweight metal alloys that can be very costly to process."
The lifecycle analysis found that 3D components use as little as one-third to one-half of the energy used in conventional methods, and are expected to reduce aircraft fuel consumption by approximately 6.4%
How well do you really know your competitors?
Access the most comprehensive Company Profiles on the market, powered by GlobalData. Save hours of research. Gain competitive edge.
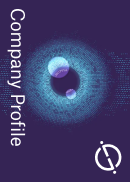
Thank you!
Your download email will arrive shortly
Not ready to buy yet? Download a free sample
We are confident about the unique quality of our Company Profiles. However, we want you to make the most beneficial decision for your business, so we offer a free sample that you can download by submitting the below form
By GlobalDataThe case study also stated that the process will save thousands of tonnes of aluminium, titanium and nickel.
"We have suboptimal designs because we’re limited by conventional manufacturing," Masanet added.
"When you can make something in layer-by-layer fashion, those constraints diminish."
The 3D printing process has certain issues with surface quality, residual stresses, repeatability and throughput for full-scale adoption that can be tackled by further research, the researchers added.
Image: Northwestern University Morris E Fine junior professor Eric Masanet. Photo: courtesy of Robert R McCormick School of Engineering and Applied Science, Northwestern University.