
Fraunhofer Institute for Production Technology (IPT) in Aachen, Germany, has developed a new clamping system that helps aircraft turbine manufacturers tackle vibration issues during processing.
Turbine blades are mounted on compressor disks, which are milled from a single piece of material, unlike the previous blade by blade construction.
Named ‘blade-integrated disks,’ the compressor disks are designed to compress air in the turbine.
As turbine blades are long and thin, the manufacturing process involves certain problems such as to vibration, which will hamper further works. Tension on the turbine blades will slightly distort their geometry, researchers said.
Consequently, manufacturers prefer to follow a step-by-step approach, first processing the outer edge of the blade then carry out precise finishing work.
The clamping system features spring-loaded clamps, which grab the blade with equal tension on both sides, and once the elements are in place, they are hydraulically clamped to hold the workpiece.
How well do you really know your competitors?
Access the most comprehensive Company Profiles on the market, powered by GlobalData. Save hours of research. Gain competitive edge.
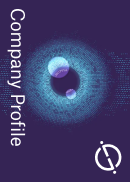
Thank you!
Your download email will arrive shortly
Not ready to buy yet? Download a free sample
We are confident about the unique quality of our Company Profiles. However, we want you to make the most beneficial decision for your business, so we offer a free sample that you can download by submitting the below form
By GlobalDataIPT engineer Roman Kalocsay said: "With the clamping system, absorption in titanium blisks is 12.5%.
"Without it, absorption falls to just 0.027%."
The system is claimed to help reduce manufacturing costs by €5,000 per blisk.
If the edges of a blade appear to be frayed, manufacturers can reuse the material using laser metal deposition and mill it to the desired form; however, the workpieces should be evaluated first, as it is not clear how much they may have drifted to the left or right.
Kalocsay added that the clamping system will also help in this scenario.
"It doesn’t change the blisk’s geometry by even a micrometre," Kalocsay added.
"The blade is fixed in place in just a few seconds and can be worked on immediately."
Image: The three-part clamping system holds the blisk blades. Photo: courtesy of Fraunhofer IPT.